Supply chain disruptions pose formidable challenges to businesses of all sizes, but Small and Medium-sized Enterprises (SMEs) often find themselves in a particularly vulnerable position. Constrained by limited resources, SMEs face a unique predicament when it comes to responding and recovering from logistics disruptions. These challenges, which span from streamlining production processes to managing inventory efficiently, affect SMEs at various stages of their operations. Notably, the lack of real time supply chain visibility into the movement of goods stands out as a critical area of vulnerability, capable of impeding logistics in multiple ways.
Small and medium-sized enterprises often lack the resources to invest in direct integrations with all the carriers they employ. Therefore, they should consider harnessing third-party solutions. Additionally, SMEs may not always have the means to implement a comprehensive ERP system, which is why opting for a solution with a user-friendly interface is advisable. This approach allows them to initiate operations swiftly without waiting for time-consuming integrations to be completed.
Within the confines of their limited resources, SMEs possess a distinct advantage – their agility and adaptability. In this blog, we'll delve into how SMEs can leverage these traits further by harnessing the power of real-time supply chain visibility, turning it into a potent tool that levels the playing field and empowers them to compete effectively with large enterprises.
How the Lack of Real Time Supply Chain Visibility Affects SMEs More?
Imagine a small manufacturer producing a limited quantity of a highly specialised product. Every component in their inventory is precious, and any delay in the supply chain can spell disaster. Without real time transportation visibility, they are at the mercy of unforeseen disruptions, such as port congestion, customs delays, or extreme weather conditions.
For a large corporation, such hiccups might be absorbed as minor setbacks. But for SMEs, these disruptions can quickly cascade into operational nightmares. They might not have the financial buffer to absorb additional costs or the surplus inventory to meet unexpected demand surges, making them more susceptible to production stoppages, stockouts, and lost sales.
Trust holds a more significant position in the interactions between SMEs and their customers compared to the relationships between two large organisations. Consequently, if there are delays in SME operations, it can carry greater significance due to the heightened importance of trust in these connections.
Challenges Due to Lack of Supply Chain Visibility in SMEs
The challenges SMEs face are distinctly different compared to their larger counterparts. Here, we dissect the many ways SMEs grapple with the lack of real time supply chain visibility into their operations, unearthing the unique hurdles they face.
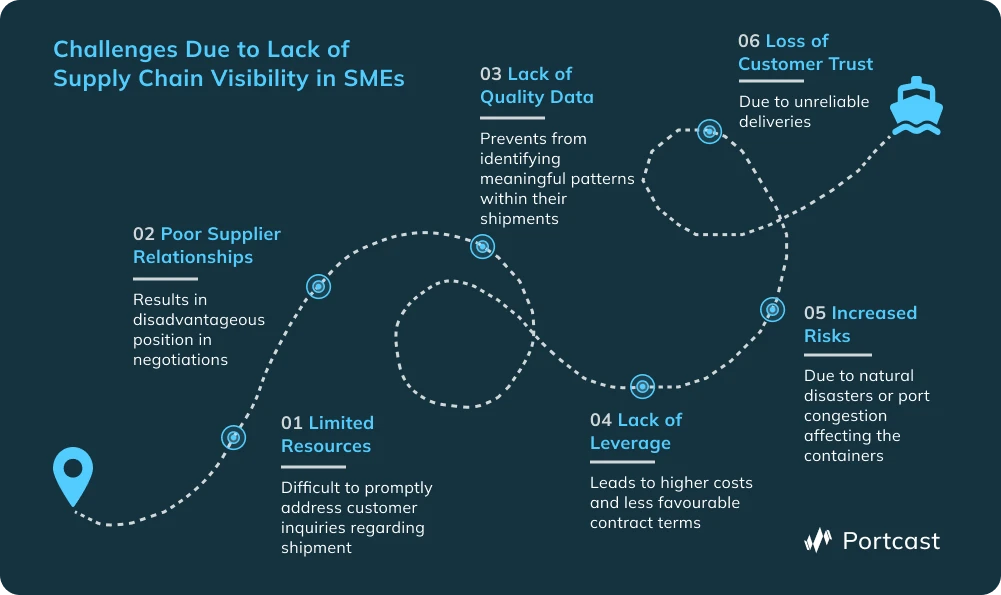
Limited Resources
SMEs, by nature, operate with comparatively fewer resources at their disposal. This particularly holds true when tracking goods in transit, promptly addressing customer inquiries regarding shipment status, and effectively managing disruptions. Often grappling with disconnected systems, their operational limitations make it challenging to respond to disruptive scenarios proactively.
Poor Supplier Relationships
Supplier relationships are inherently complex, with potential conflicts regarding invoicing, payments, shipment punctuality, etc. SMEs, overshadowed by their larger counterparts, often find themselves in a disadvantaged position when engaging in negotiations with their suppliers. This susceptibility in supplier relations can initiate cascading consequences across the supply chain, affecting SMEs to a greater extent.
Lack of Quality Data
SMEs often rely on conventional tracking methods, such as spreadsheets, manual communication via email and phone calls with freight forwarders, or direct checks on carriers' websites. Apart from being exceedingly time-intensive, this method also lacks the critical element of real-time data insights regarding their shipments.
For instance, an SME may lack comprehensive analytical insights to discern meaningful patterns within their shipments, which could otherwise aid in mitigating warehouse and inventory issues and enhance demand forecasting. This absence of dependable transportation visibility data is a driving factor behind inventory challenges and can adversely impact cash flow and customer satisfaction.
Lack of Leverage
SMEs commonly have restricted bargaining power when engaging with suppliers and carriers. This disparity typically leads to higher costs and less favourable contract terms than their larger corporate counterparts. Moreover, SMEs are vulnerable to supply chain disruptions when reliant on a constrained pool of suppliers or carriers. The dependency on a limited number of suppliers for crucial materials exposes SMEs to significant risks, especially when those suppliers encounter their own supply chain disruptions.
Risk Management
Identifying and mitigating risks, such as natural disasters, political instability, or port congestion, is complex for SMEs. They often lack the financial cushion that larger enterprises enjoy, making these unexpected transportation delays caused by disruptions more financially straining. These delays can increase operational costs, eating into already tight budgets.
Customer Relationship
Customer relationships are highly important for SMEs. Loss of customer trust due to unreliable deliveries can be harder for SMEs to rebuild compared to larger corporations.
Assumptions Held by SMEs Regarding Supply Chain Visibility Solutions
Why Real Time Supply Chain Visibility Matters to SMEs
Small and Medium-sized Enterprises (SMEs) are increasingly becoming integral players in the global business network, participating in multifaceted supply chains where they assume diverse roles as suppliers and customers. The significance of supply chain visibility in the context of transportation holds immense relevance for SMEs.
Here's why:
1. Provides real-time container tracking insights into product locations and expected delivery times, reducing communication gaps and enhancing logistics planning.
2. Aids in data-driven supplier selection, enabling improved terms, reliability, and potential cost savings.
3. Enhances data quality, providing a competitive edge during negotiations with stakeholders such as carriers and suppliers.
4. Helps optimise inventory levels and ensure products are available when and where needed.
5. Essential for business continuity, aiding better decision-making through analytics, which enhances customer satisfaction while reducing bottlenecks.
6. Empowers SMEs to set accurate customer expectations, cultivating loyalty—proactive communication about potential delays and preemptive measures foster customer trust and satisfaction.
7. Provides easy access to transit time data, enabling SMEs to meticulously plan routes, carriers, and modes, optimising their costs.
8. Real-time tracking data is accessible across the organisation, benefiting various teams, from customer service and finance to sales and marketing. This broad access improves efficiency and responsiveness.
9. Enables real-time adjustments, empowering SMEs to modify routes or even switch modes for critical deliveries.
10. Supply chain visibility equips SMEs to scale effectively, ensuring that their supply chain processes and infrastructure can accommodate growth while maintaining operational efficiency.